
Image Credit: Steve's Junk
A Brief Review Of Electrochemical And Electrodischarge Machining
EDM and ECM processes are advanced manufacturing technologies with unique capabilities due to their non-mechanical material removal principles can be found in different areas of application in industry offering a better alternative or sometimes the only alternative in generating accurate 3D complex shaped macro, micro and nano features and components of difficult-to-machine materials.
Introduction
Electrochemical Machining (ECM) is a non-traditional machining (NTM) process belonging to Electrochemical category. ECM is opposite of electrochemical or galvanic coating or deposition process. Thus ECM can be thought of a controlled anodic dissolution at atomic level of the work piece that is electrically conductive by a shaped tool due to flow of high current at relatively low potential difference through an electrolyte which is quite often water based neutral salt solution.
On the other hand, Electrical Discharge Machining (EDM) is a controlled metal-removal process that is used to remove metal by means of electric spark erosion. In this process an electric spark is used as the cutting tool to cut (erode) the workpiece to produce the finished part to the desired shape.

Wire EDM beginnings in 1969, the Swiss firm Agie produced the world’s first wire EDM. Image Credit: Pinterest
Challenges Of Machining
The demand for macro- and micro- products and components of difficult-to–machine materials such as tool steel, carbides, super alloys and titanium alloys has been rapidly increasing in automotive, aerospace, electronics, optics, medical devices and communications industries. In spite of their exceptional properties, many of these difficult-to-machine materials seem to have limited applications. These materials pose many challenges to conventional machining processes (such as turning and milling).
For example, titanium alloys are susceptible to work hardening and its low thermal conductivity and higher chemical reactivity result in high cutting temperature and strong adhesion between the tool and work material leading to tool wear. Electrical Discharge Machining (EDM) and Electrochemical Machining (ECM) offer a better alternative or sometimes the only alternative in generating accurate 3D complex shaped features and components of these difficult –to- machine materials.
Advantages of ECM
One of the major advantages of ECM is the scalability of the process with the use of multiple electrodes on the same machining setup. ECM using multiple electrodes machined to machine arrays of micro holes results in increased productivity. Taper induced on the workpiece during ECM drilling is a major concern. Some of the tool designs for the reduction of taper include dual pole tools, insulated tools, and tools with shaped ends.
High conductivity, heat resistance and high melting point are the main desired properties for an EDM tool. The most common materials used in EDM tooling are copper, graphite, tungsten and tungsten carbide. Research is being done on many new materials including composites for EDM tooling.
Typical as well as innovative examples of application for the most important areas of application – die and mold manufacturing, turbomachinery component manufacture, tooling and prototyping and medical engineering. In addition, combined and even hybrid EDM and ECM processes are known with superior overall process performance.
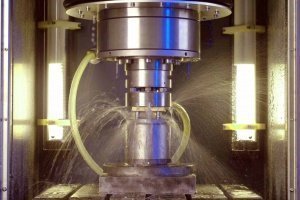
Electro-Chemical Machining (ECM) with up to four Axes. Image Credit: Pinterest
In all areas of application, the final surface integrity defines the later part performance. Therefore, the machining processes have to be designed and executed in such a way that the specific operation demands are fully met by the remaining surface modifications of the machined part. From application point of view different manufacturing processes could only compete with each other when providing at least the same part functionality and therefore similar material modifications.
Summary
While EDM incorporates thermal energy dissipation, ECM purely relies on a chemical material removal principle. ECM and EDM technologies have been successfully adapted to produce macro, micro components with complex features and high aspect ratios for biomedical and other applications. These processes are also being attempted at the nano-scale.