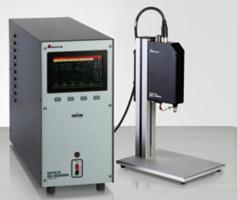
High-Precision Spot Welding Improves Process Control
Richard Barber explains high-precision micro-joining applications like implantable medical devices, high-frequency inverter resistance spot welding technology provides closed-loop feedback for exceptional process control is not as daunting as one would assume.
This powerful welding functionality need not be difficult to implement and operate. In fact, advanced technology packaged with intuitive interfaces and full connectivity to production management systems make state-of-the-art systems simpler and more versatile.
This enables Research and Development (R&D) laboratories and production facilities to achieve more consistent output across diverse applications and between multiple welding stations. The closed-loop feedback also enables automatic adjustments to compensate for variability in part geometry and thermal loading characteristics.
Keeping things simple and well-connected opens up possibilities for a wide range of applications and exponentially expands the utility and value of technology. One of the world’s largest medical device companies recently implemented a welding solution that affords this combination of high functionality, versatility, and simplicity. Each welding station, consisting of a power supply, weld head, and weld monitor, functions as a fully-integrated unit.
The production management system reads a bar code and interrogates a database to select the weld profile, which is sent to the welding station via an Ethernet connection. The welding station then displays the weld profile data to the user with information about the application, parts, and tooling, ensuring production integrity.
Flexibility Matters
The flexibility of this solution is critically important. The medical device industry is subject to stringent validation requirements. Once calibration procedures and other validation requirements have been completed in the R&D laboratory, it is highly beneficial to be able to use existing tools and processes in the production environment.
Read more here
What You Missed:
wire and Tube 2024 To Set New Standards
Elon Musk Announces First Neuralink Wireless Brain Chip Implant
IMF: AI To Hit 40% Of Jobs And Worsen Inequality
GM’s Cruise Faces Federal Investigations After Accident Involving Pedestrian
AI Chatbot Disabled After Writing A Self-Scathing Poem About Company
ALI Technologies’ Flying Bike Fails To Take Off
Metal Prices To Ease With Softening Demand According To World Bank
Hyundai Mobis Unveils MOBION Featuring e-Corner System That Enables Sideway Movement
CES 2024 Showcases Latest Innovations In AI, Sustainability And Mobility
Tesla Dethroned By BYD As World’s Best Selling EV Maker
Quang Ninh Industrial Zones Face Electricity Shortage
WANT MORE INSIDER NEWS? SUBSCRIBE TO OUR DIGITAL MAGAZINE NOW!
CONNECT WITH US: LinkedIn, Facebook, Twitter
Letter to the Editor
Do you have an opinion about this story? Do you have some thoughts you’d like to share with our readers? APMEN News would love to hear from you!
Email your letter to the Editorial Team at [email protected]