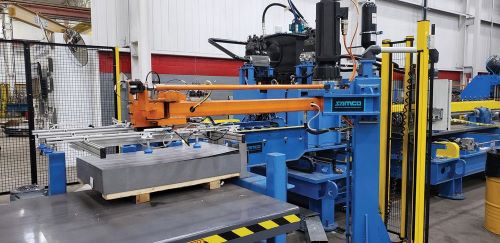
Up Your Roll Forming Game With Samco Machinery
Jaswinder Bhatti, Vice President of Applications Engineering from Samco Machinery Ltd explains how front- and back-end automated material handling systems for roll forming can quickly and safely process parts.
Roll forming systems used to run at a very slow speed, about 50 ft (15m)/min., making it easy to handle everything manually at the end of the line. These days roll formers can run anywhere from 300 (91m) to 500 ft (152m)/min. Speed can make parts hard to handle, so does part configuration, which has become more complex as machine capabilities have expanded.
Typically, parts were roll-formed and additional features and processes were incorporated manually down the line. Today’s roll forming systems can include some punching, forming, bending, and other processes that have nothing to do with roll forming itself, and are designed for complete, done-in-one part manufacturing. Following these systems are sophisticated material handling automation.
Moving from one process to another, automated material handling eliminates human error, particularly as it relates to part orientation. Automation helps verify that the correct part is being handled and orients it for proper processing. It also helps to reduce the dependency on an operator, which increases roll forming uptime and speed.
A material handling system can process parts much faster than any operator can, especially when the parts on the line are large and heavy. Manually moving and orienting these parts repeatedly throughout the day opens operators up to fatigue and injuries.
Time savings is another benefit of an automated material handling system, especially with packaging and nesting. An operator can sometimes lose count of part runs, and shipments can go out with inaccurate orders.
The ability to count part runs to ensure orders are completed correctly saves time, both on the front end with inventory and in ensuring orders will not need to be reproduced and reshipped. COVID-19 also has demonstrated additional benefits of automated material handling systems.
Fabricators are required to follow strict protocols for limiting the number of people in a workspace and maintaining proper distancing. These systems reduce the number of workers needed to run the roll forming equipment, maintaining safety standards.
What You Need to Know
Most shops have limited space on the shop floor, and incorporating automated material handling equipment can take up more space than what is currently allotted, so a restructuring of equipment might be needed. This takes careful planning, especially if there are secondary processes involved.
Some shops might not see the initial value in adding such a system, especially with the upfront costs. But the machine does not take breaks and will continue at the same processing rate throughout the day. By removing the human element and maintaining consistency of the process, fabricators can expect significant throughput gains, sometimes upwards of 35%.
Read more here at page 32
What You Missed:
wire & Tube China 2024 Pre-registration Opens!
AI Has Crept Its Way Into Aerial Combat
Tesla Profits Decline By More Than 50% In Q1 2024
Tesla Reduces Full Self-Driving Software Price To US$8,000
Researchers Turn Metal Waste Into Catalyst For Hydrogen
Is AI Is Looking More Like A Band Aid Now?
Rever Automotive Builds And Tests BYD Buses In Thailand
Tesla Cuts More Than 10% Of Its Workforce
Tesla Settling Lawsuit Erodes Faith In Autonomous Driving
IoT Offers A Wealth Of Opportunities
WANT MORE INSIDER NEWS? SUBSCRIBE TO OUR DIGITAL MAGAZINE NOW!
CONNECT WITH US: LinkedIn, Facebook, Twitter
Letter to the Editor
Do you have an opinion about this story? Do you have some thoughts you’d like to share with our readers? APMEN News would love to hear from you!
Email your letter to the Editorial Team at [email protected]