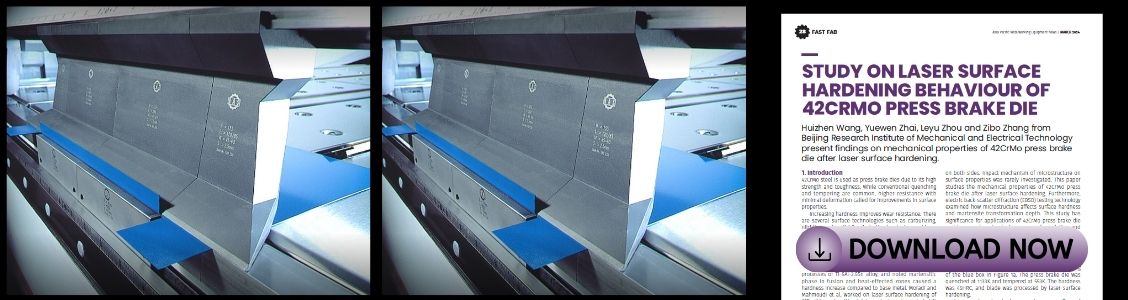
Study On Laser Surface Hardening Behaviour Of 42CrMo Press Brake Die
Study On Laser Surface Hardening Behaviour Of 42CrMo Press Brake Die
Huizhen Wang, Yuewen Zhai, Leyu Zhou and Zibo Zhang from Beijing Research Institute of Mechanical and Electrical Technology present findings on mechanical properties of 42CrMo press brake die after laser surface hardening.
Introduction
42CrMo steel is used as press brake dies due to its high strength and toughness. While conventional quenching and tempering are common, higher resistance with minimal deformation called for improvements in surface properties. Increasing hardness improves wear resistance.
There are several surface technologies such as carburizing, nitriding, carbo-nitriding, induction hardening, and laser surface treatment. One promising surface technology is laser surface hardening, which ensures high accuracy, thermal concentration and processing speed, and low heat input. It can significantly enhance surface hardness and wear resistance.
Khorram and Junaid et al. investigated laser surface processes of Ti-5Al-2.5Sn alloy, and noted martensitic phase in fusion and heat-effected zones caused a hardness increase compared to base metal. Moradi and Mahmoudi et al. worked on laser surface hardening of AISI 420 martensitic stainless steel, and concluded it increases hardness and corrosion resistance.
Levcovici et al. reported hardness of austenitic stainless steel with laser surface hardening was 2.5 to 3 times higher than base material’s. Lee and Telasang et al. studied laser surface hardening behaviour of AISI H13 tool steel and results revealed enhanced hardness and wear resistance.