
Shifting Gears: Addressing New Requirements In EV Manufacturing
Shifting Gears: Addressing New Requirements In EV Manufacturing
Andy Kuklinski of Ceratizit talks about the electric vehicle trend in the automotive industry, how it has changed the machining landscape, and the new requirements being faced by manufacturers. Article by Stephen Las Marias.
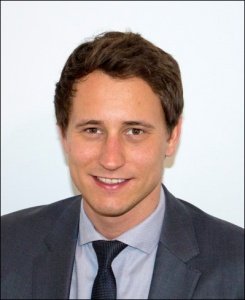
Andy Kuklinski
The Ceratizit Group develops and produces highly specialised cutting tools, indexable inserts, rods made from hard materials, and wear parts. Active in more than 80 countries worldwide, the Group has more than 8,000 employees and over 30 production sites. Its innovative hard material solutions are used in various sectors, including mechanical engineering and toolmaking, wood and stone working, in the automotive and aerospace industries, and in the oil, gas and medical industries.
In an interview with Asia Pacific Metalworking Equipment News, Andy Kuklinski, Head of Segment Automotive/Team Cutting Tools at Ceratizit, talks about the electric vehicle trend in the automotive industry, how it has changed the machining landscape, and the new requirements being faced by manufacturers.
HOW HAVE THE REQUIREMENTS IN ELECTRIC VEHICLES (EVs) CHANGED THE AUTOMOTIVE MANUFACTURING LANDSCAPE?
Andy Kuklinski (AK): One of the changes is that even more components will be made of aluminium. This will affect and change the manufacturing and supplier strategy. A typical example are cylinder heads and cylinder blocks. While these parts used to be manufactured mainly by the OEMs themselves, the focus is now moving to Tier 1 and even Tier 2 suppliers for the machining of the electric engine casing. We are increasingly seeing former aluminium foundries now responding and manufacturing the finished machined part in the same production facility. So, the landscape, especially the supply chain landscape, will definitely look different towards EV manufacturing.
WHAT KEY CHALLENGES HAVE YOU BEEN HEARING FROM YOUR AUTOMOTIVE CUSTOMERS WHO ARE TRANSITIONING TO EV?
AK: We are in constant exchange with our customers and hear again and again how challenging it is to react to the enormous and rapid changes in automotive components. In particular, the R&D and production planning departments are under great time pressure to meet the massively increasing demand for EVs. By supporting them quickly with the right machining concepts, we can mitigate at least some of this pressure.
HOW DO THESE CHALLENGES DIFFER FROM THE TRADITIONAL INTERNAL COMBUSTION ENGINE VEHICLES?
AK: For one thing, the time pressure was much less with the combustion vehicles, since it was not necessary to renew large parts of the portfolio in a short period of time. The product cycles were very finely tuned. For another, the parts that are being created now, especially in the powertrain area, are completely different from the parts that car companies produced in the past—many things are still new and simply bring new challenges. Previous combustion engines were always developed in a similar way and always had the same contours and materials that people knew how to process. In many respects, it was a constant process of optimisation.
HOW ARE THESE CHALLENGES IMPACTING YOUR TECHNOLOGY/PRODUCT DEVELOPMENT STRATEGIES?
To continue reading this article, head on over to our Ebook!
Check these articles out:
Automotive, Electrical/Electronics Industries Driving Global Industrial Robotics Market
A Look At Global Powertrain Key Technologies And Trends by Region
IDTechEx Report Reviews How Nickel Is Replacing Cobalt In Electric Vehicles
3D Printing Solutions for the Automotive Industry
Electric Cars May Be Cheaper Than Petroleum Cars In Seven Years
For other exclusive articles, visit www.equipment-news.com.
WANT MORE INSIDER NEWS? SUBSCRIBE TO OUR DIGITAL MAGAZINE NOW!
FOLLOW US ON: LinkedIn, Facebook, Twitter