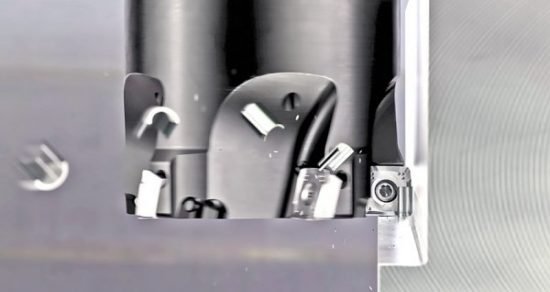
A Fresh New Coat For Inserts
A Fresh New Coat For Inserts
Both CVD and PVD coatings for metal cutting inserts are seeing continuous improvements for adhesion, toughness and wear properties. By Jonathan Chou
Indexable inserts are most often used in cutting tools. These replaceable attachments contain the cutting edge, and are commonly coated in two ways: chemical vapour deposition (CVD) and physical vapour deposition (PVD).
With a thicker coating, CVD inserts are generally more wear-resistant, making them useful for high-speed machining and turning. PVD inserts typically have thinner coatings suited for stainless steels that might chip cutting edges. Both types of coatings are seeing constant optimisations for adhesion, toughness and wear properties.
Roaring New Standard

Walter’s Tiger tec Gold WKP35G is suitable for milling steel and cast iron materials.
The Tiger tec Gold is the latest in Walter’s line of coated indexable inserts. Preceded by Tiger tec and Tiger tec Silver, the new coating is more resistant to wear and, at the same time, process-reliable. The reason for that is due to a significantly higher aluminium content of 85 percent.
This was achieved by developing a process called ULP-CVD technology. In a combination of ultra-low pressure (ULP) and CVD, the developers in Tübingen separated TiAlN (titanium aluminium nitride), the basis for manufacturing the new grades. In addition to TiAlN as the main coating, the new WKP35G grade also uses TiN. With its golden colour, it also provides the name for the new coating.
Jörg Drobniewski, head of cutting material development at Walter AG, mentioned that they carried out around 50 extensive test runs with customer applications since spring last year.
The company found that indexable inserts coated with Tiger tec Gold WKP35G had higher wear resistance on flank faces, lower rate of hairline cracks forming and improved resistance to plastic deformation, resulting in increased tool life.
“The golden colour has the added welcome effect that it is now much easier to detect wear than it was in the past,” said Wolfgang Vötsch, senior product manager for milling at Walter.
Currently, the Tiger tec Gold WKP35G grade for milling steel and cast iron materials is available and other grades will soon follow.
Navigating Tricky Paths
Complex tool paths or difficult-to-machine materials can cause edge line chipping that leads to poor surface finish and tool failure. Indeed, milling some of the more ‘tacky’ materials in the ISO P classification can cause flaking of the insert coating, which in turn leads to breakage of the edge line.
Thermal fluctuations, especially during machining under wet conditions, can cause crack formation, an undesirable effect that tends to induce unpredictable tool life or even sudden breakage.
Sandvik Coromant has developed a new PVD coating grade called GC1130 using a production technology called Zertivo, and the company states that the whole insert is taken into consideration, not just the coating.
The addition of high chromium content substrate in the cemented carbide helps withstand edge-line chipping and cracks arising from difficult machining environments, such as temperature and/or load variations, as well as vibrations.
The GC1130 range will be first introduced with inserts in sizes 07 and 11, although further extensions are planned to follow.
Interrupted Cutting

Pramet’s T7325 grade is matched for stainless steel. It was developed to complement their existing T7335 grade.
The newly launched T7325 grade from Pramet is suitable for machining of stainless steels. It has been developed to complement the existing T7335 grade, which is recommended for use in unstable machining environments.
Also suitable for interrupted cutting, the latest T7325 grade features a functional gradient substrate and special modern titanium and CVD coating.
This combination offers high cutting strength, reduced built-up edge and resistance to the formation of cracks. As a result, the grade provides higher of operational reliability, performance and tool life.
New Cutting Tool Materials For Cast Iron
Kyocera’s recent CA3 series has longer tool life and consistent processing of cast iron through a newly developed CVD coating with a pink-gold finish over a carbide base metal. The series also has redesigned blade-edge shapes.
There are three types of inserts within the CA3 series: CA310, CA315 and CA320. CA310 is focused on wear resistance for machining grey cast iron through the deposition of a thickened aluminium oxide coating. This makes it suitable for high-speed continuous machining.
CA315 is suited for machining grey and nodular cast iron by optimising the total coating layer thickness, making it recommended for general machining.
CA320 has improved stability in heavily interrupted machining for nodular cast iron by utilising a thin CVD coating.
Finding The Right Insert
Solid cutting tools require manpower hours to be sharpened. For indexable inserts however, you only need to flip or turn the insert to a new edge or replace a worn insert with a brand new one, saving yourself time.
As indexable cutting tool technology continues to improve, better productivity will be seen with longer, more predictable tool life and higher metal removal rates.
APMEN Metal Cutting