
When Precision Touches Flesh and Blood
Arno: When Precision Touches Flesh and Blood
In producing surgical instruments, Eberle Medizintechnik only trusts ARNO’s tools. Here’s why. Article by ARNO Werkzeuge.

Bursting at the seams and soon to relocate to a new building: production at EBERLE in Wurmberg.
To put it bluntly, everyone is much happier when they do not need products from Eberle Medizintechnik. Well, not as such. On the other hand, they are extremely welcome when it comes to minimal invasive surgery and operations. However, then they must meet the highest standards with regards to functionality, quality and sterilisation. For many years, ARNO Werkzeuge has been a reliable partner servicing the requirements of Eberle with high-quality tools and a tool management system. This ensures that precision remains second nature when it is a matter of flesh and blood.
“We need the highest precision and best surface qualities for our surgical instruments,” emphasises Bernd Amann, Technical Director at Eberle GmbH & Co. KG. “ARNO Werkzeuge is an excellent partner who backs us up with consultation and products.”
The sheer amount of quality know-how incorporated at Eberle only comes to light after a brief look at their production depth. The company even makes its own cables and connectors. So, it is no wonder that experts also call on professionals for cuttings tools to manufacture medical instruments of the highest quality and functionality as well as their consulting services.

Instruments made by EBERLE are used in minimally invasive surgical treatments and operations.
Maintaining Quality
The Eberle product portfolio comprises about 1,000 products manufactured to a production depth of almost 100 percent. This mainly includes shaver blades for arthroscopies, surgical and urological operations, or ENT operations and drills, sawing blades and wires including the associated drive systems and hand instruments. High quality is most apparent in the shaver blades. Guide tubes and internal tools are produced in a number of turning, grinding, laser welding and sometimes hardening operations. For example, tool tips are eight millimetres long with diameters of 4.5 mm or 3.5 mm. Together with the openings for cutting tools, they are welded to the tubes in a laser welding process. The drilling and cutting tools rotate inside the guide tubes. As expected, Eberle also produces the gear wheels on the cutting heads. The superior machine pool includes lathes for Swiss and fixed headstock machining from Star, Boley and Index and a five-axis milling centre from Chiron, vertical eroding and wire EDM machines, grinding machines and laser welding machines.
Since Eberle was founded in 1999, the company has used turning, grooving, drilling, and milling tools from ARNO Werkzeuge. They are looking forward to relocating their production to a new building in the foreseeable future as the present facilities are bursting at the seams. The company uses nine different VHM milling cutters, eight different SA grooving tools, the AKB drilling system, and eleven types of ground high-positive indexable inserts from ARNO Werkzeuge.
“In particular, the high-positive indexable inserts impress us time and again since they produce extremely good surface finishes and have long tool lives,” Amann assures.
ARNO sales engineer Alexander Rentschler explains, “These specially developed high-positive chip geometries achieve optimum machining results by using high-performance cutting materials—also because they produce less vibration during the turning process. Not only that, the polished surface optimises chip evacuation and the ground circumference ensures very high accuracy.”
“The finish quality is so high that some downstream process steps are no longer necessary,” Amann says. This is also a key factor in minimising the adhesion of germs to products which are later cleaned and sterilised.
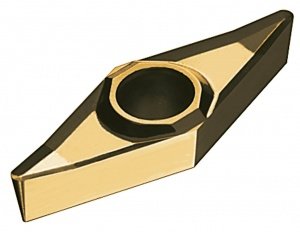
High-positive indexable inserts from ARNO Werkzeuge achieve top finish quality by optimising chip evacuation due to their ground circumference and polished surfaces.
Addressing ENT Instrument Requirements
Amman relies on SA modules from ARNO Werkzeuge for grooving work. Among them are modules with inserts chamfered at 15 deg for grooving thin-walled tubes.
“The tubes are mainly used for our shaver blades for ETN operations,” says Amman. The sturdy, narrow grooving blades which ARNO offers for cutting depths of 10 to 70 mm and grooving widths of 1.5 to 8 mm are the optimum solution for him “since they ensure high process reliability. And that’s important for us since our series are not very large.” A series may range from five to 5,000 units and batches are manufactured in volumes of maximum 500 units. “This means we cannot afford to have any rejects,” he adds.
ETN instruments are very special products. After the guide tubes are manufactured, they are bent at radii of 50 deg to 65 deg. Of course, the drive inside the tubes must play along. In this case, Eberle uses small drive elements which transfer rotational movement via spur gears. Up to nine bevel gears of this type are mounted in an instrument. The instrument must also accommodate a flushing duct.
“Here, we are talking about internal diameters of only a few millimetres,” says Amann. It is only by applying this solution that allows bent Eberle ETN instruments to rotate at 12,000 rpm for maximum half an hour before the single-use instruments are disposed of.
Perfect Tool Management System
Eberle has opted for the StoreManagerPRO from ARNO Werkzeuge for its tool management system. A footprint of only 1.5 square metres is all it takes to store and manage tools in up to 2,160 compartments. At present, Eberle still uses it for approximately 600 to 700 tools including gauges, as well as keys for the vehicle fleet, as an employee says with a grin.
“That’s not so unusual,” says Simon Lang, product manager of Tool Management Systems at ARNO Werkzeuge. “In fact, it’s an excellent way to track who is currently driving which vehicle for what purpose.”
Amann intends to expand the options since he is convinced by the modular system that allows controlled single withdrawal and re-storage. “With the ARNO StoreManagerPRO, we benefit from smooth functioning tool management, tracing and restocking – and this raises the efficiency of our internal production processes,” he says. Amann also appreciates that the tool management system can be flexibly configured; it is extremely robust, easy to operate and operational round the clock. The system offers many options for customising the software and configuring the maximum 2,160 compartments. It makes tool management and repurchasing simpler and more efficient. Order proposals can be produced easily and straightforwardly for the purchasing department at any time or order procedures can be initiated to any number of suppliers. The practical orientation of the software design permits users to conveniently edit data from a workplace PC. One feature that is particularly well received is that the StoreManager can also manage third-party tools, “since of course, we also use products from other manufacturers,” says Amann, explaining standard practice at the company.
Eberle not only manufactures endoscopic and surgical instruments, it also supplies the associated control units together with the software and housings, as well as the cables and connectors. So, Eberle is not only inside the products on which the name of Eberle appears, Eberle is also integrated in many products made by renowned German manufacturers and market leaders in their segments. “We have been making private label products for them for years,” explains Managing Director Frank Eberle. “Together with ARNO Werkzeuge, this has worked out well for many years “because quality and consulting also come as second nature to us,” he concludes.
Check these articles out:
HAIMER To Showcase Latest Technologies And Solutions At EMO 2019
Nissin Electric To Move Production From Thailand And Vietnam To Myanmar
EMO Hannover 2019: Global Machine Tool Community Paving The Way For Industry 4.0
OnRobot Wins Gold in LEAP Awards
Hexagon Touch Probe Transforms Thickness Measurement on Machine Tools
heimatec to Showcase New Tool Features and Innovations at METALEX 2019
WANT MORE INSIDER NEWS? SUBSCRIBE TO OUR DIGITAL MAGAZINE NOW!
FOLLOW US ON: LinkedIn, Facebook, Twitter