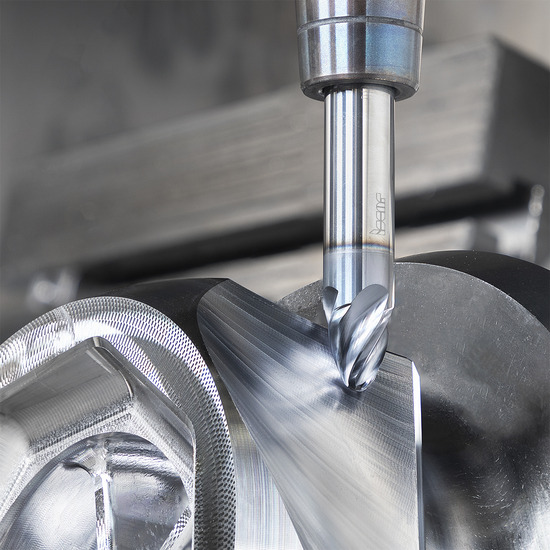
ISCAR’s Promising Segment With Five Axis Machining
ISCAR explains how their five-axis machining can be simpler when paired with an optimum portfolio of milling tools.
Five axis machining is increasingly popular in modern metal cutting. It provides significant advantages such as machining complex-shaped parts by use of one set-up without changing the location of the workpiece, high machining accuracy, and reduced cycle time.
A Layer Deeper
Advanced technology of workpiece fabrication has led to increased capabilities of precise forging, casting, and mainstreaming additive manufacturing (AM). This resulted in the increased complexity of workpiece geometry, decreasing machining allowance and material by cutting operations and achieving end results which reflect the final shape of the workpiece.
The requests for high-performance cutting tools intended for finishing and semi-finishing geometrically complex surfaces are now vitally important. Ball-nose milling cutters are considered traditional tools for machining 3D surfaces.
Ball-nose cutters are the most common tools for semi-finishing and finishing profile in milling operations. Progress in the field of five-axis machining centres, and a significant step forward in modern CAM systems have emerged tools with a different cutting geometry, referred as segment or barrel-shape endmills.
Even though these tools are well known to machinists, they remain ignored. Five-axis machining combined with CNC software and computer modeling of complex tool configurations reemerged the use of circular segment endmill applications.
In All Directions
The cutting edge of these endmills is an arc that represents a segment of a circle with a radius larger than the nominal radius of a tool. For comparison purposes, in ballnose cutters the tool radius is the radius of the cutting edge.
Machining surfaces using ‘passes technique’ segment-type endmills enables a substantially increased step size compared to ball-nose cutters, thus reducing the cutting time. A three-axis CNC controlled cutting process cannot guarantee the correct position of a barrel shaped cutting tool when machining complex surfaces.
The five-axis machining concept allows taking full advantage of segment endmills. Depending on the orientation of the cutting edge relative to the tool axis, segment endmills possess various configurations such as pure barrel, tapered barrel, lens, and oval or parabolic shapes.
The form of the tool cutting edge determines the tool application. For example, lens-shaped tools are suitable for both five and three-axis machines, while endmills with a tapered barrel profile are intended for five-axis machines.
Segment cutter designs appear in multi-flute solid endmills that deliver ultimate tool accuracy and maximise the number of teeth on the cutting tool.
Read more here —–> https://t.ly/9yqt
Related Stories:
Solutions For Micro Machining And Swisstype Turning For Precision And Tolerance
Paul Horn’s All-Rounder For Slot Cutting And Groove Milling
Machining Composites As Fine As Paul Horn
Pre-Fabricate Large Workpieces With Precision
How Precision Machining Allows Adaptability To Complex Challenges
Metalworking Fluids Market Outlook By Industries And Areas
The Investigation Status Quo of the Environmental and Free-Cutting Brass
Panasonic Ceases Thailand’s 12-Volt Lead Acid Auto Battery Production
Indonesia’s Trimegah Bangun Persada Plans Expansion In Nickel Processing After IPO
Confidence Strong For China’s Recovery In Steel Sector
WANT MORE INSIDER NEWS? SUBSCRIBE TO OUR DIGITAL MAGAZINE NOW!
CONNECT WITH US: LinkedIn, Facebook, Twitter
Letter to the Editor
Do you have an opinion about this story? Do you have some thoughts you’d like to share with our readers? APMEN News would love to hear from you!
Email your letter to the Editorial Team at [email protected]