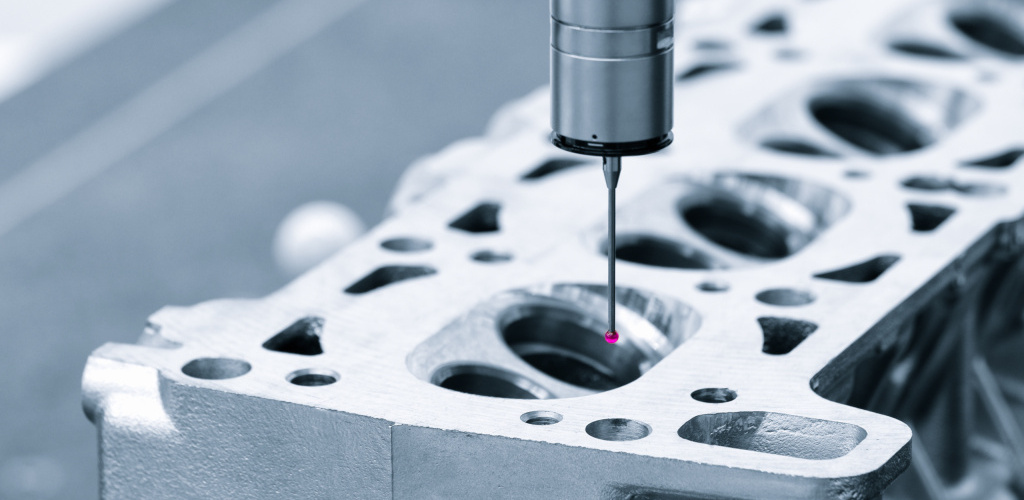
Photo: Matveev_Aleksandr
Modern CMMs In The Age Of AI And Cloud
Coordinate Measuring Machines (CMMs) have long been essential to manufacturing, ensuring quality and precision across industries. Although modern technologies—ranging from handheld 3D laser scanners to cloud-based digital twins—have introduced new paradigms, large-format, monolithic CMMs continue to evolve. Far from being obsolete, these “giants” are adopting cutting-edge innovations, from AI-driven inspection software to advanced CNC controls. Here’s how the classic CMM remains relevant and indispensable amid rapid changes in manufacturing technology.
Introduction
For decades, Coordinate Measuring Machines (CMMs) have served as the backbone of quality assurance in various industries, from automotive and aerospace to heavy machinery and maritime manufacturing. In an era dominated by rapid digital transformation, one might ask: Are large-format CMMs still pertinent, or have smaller, more agile solutions eclipsed them? While portable scanners, cloud-based analytics, and AI-based metrology software have undeniably changed the inspection landscape, the reality is more nuanced. Monolithic and large-gantry CMMs continue to offer unparalleled accuracy, repeatability, and functionality. They also play a pivotal role in modern design, prototyping, and quality control, particularly for expansive components where only large-scale measurement solutions suffice.
This article delves into the current state of CMM technology—highlighting advancements in computer numerical control (CNC) software, the transformative potential of AI and machine learning (ML), and the growing trend of cloud-driven manufacturing. We also explore how these machines integrate into modern workflows that involve 3D point cloud scanning, digital twins, and predictive maintenance. Despite the influx of newer scanning equipment, large-format CMMs remain highly relevant and continue to evolve alongside the rest of the industry.
The Persistence Of Large-Format CMMs
When Scale Matters
In industries like aerospace, maritime, and heavy equipment manufacturing, components can span several meters or more. From entire fuselage sections to the hull of a sea vessel, these substantial parts require precision measurements that smaller, portable devices simply cannot match. Large-format CMMs—often gantry-mounted—excel at this task. Built on monolithic granite bases or steel-reinforced frames, these machines are designed to operate with minimal vibration, maintaining sub-micron accuracy over large volumes. This structural rigidity cannot be easily replicated by handheld or robot-mounted scanners.
Evolving Designs And Materials
Traditional large-format CMMs were often criticized for their cumbersome footprint and lack of flexibility. Modern iterations address these issues by incorporating lighter materials like carbon fiber for arms and probes, reducing overall inertia and improving measurement speed. Furthermore, these machines now employ advanced drive systems, such as linear motors with air-bearing technology, significantly decreasing mechanical friction and enhancing reliability. These improvements allow large-scale CMMs to retain their hallmark precision while becoming more adaptive to today’s high-mix, low-volume manufacturing environments.
CNC Software And Automation
Integrating CMMs Into Smart Factories
One of the most transformative developments in the CMM landscape is the integration of modern Computer Numerical Control (CNC) software. By connecting to enterprise-wide networks, CMMs can participate in closed-loop manufacturing, automatically adjusting production parameters based on inspection outcomes. For instance, if a CMM identifies a dimensional deviation in an automotive engine block, the system can relay that information back to CNC machining centers. The machining centers then adapt tooling paths or cutting speeds in real time. Such synergy reduces scrap rates, speeds up production, and ensures consistent quality.
Automating Measurement Routines
Modern CNC software also simplifies measurement routines. Historically, programming measurement sequences on a large CMM was laborious, requiring specialized expertise. Advanced software now offers graphical, simulation-based programming, often with user-friendly interfaces that allow engineers to “drag and drop” measuring elements onto digital 3D models of parts. Some even incorporate AI-based algorithms that auto-generate inspection paths, selecting the optimum probing angles to minimize cycle times while maximizing accuracy. Consequently, even massive CMMs can be rapidly reprogrammed for new parts, improving turnaround time for prototyping and low-volume production.
Point Clouds, 3D Scanners, And Hybrid Metrology
Complement Or Competition?
Portable 3D laser scanners, structured-light scanning systems, and photogrammetry solutions have gained popularity for quickly capturing complex freeform geometries. These devices generate dense point clouds that can be processed in CAD software to reverse-engineer components or conduct form and surface inspections. Indeed, smaller, non-contact scanning technologies excel at capturing data from delicate or irregular shapes.
Yet, large-format CMMs haven’t simply yielded the stage. Gantry-mounted laser scanners now combine the speed of non-contact scanning with the large measurement volumes characteristic of conventional CMMs. This hybrid approach provides both macro-level geometry data and micro-level precision checks in one integrated setup. Moreover, the stable environment of a CMM (with controlled temperature and minimal vibration) ensures that laser-based scanning data is more repeatable than that from handheld devices in a shop-floor setting.
3D Point Cloud Data Conversion
High-density point clouds collected during inspection—whether through contact probes or laser heads—can be converted into polygonal meshes or parametric CAD models using powerful software suites. Leading names like HP, Renishaw, Konica Minolta, and other multinational corporations continue to invest in advanced algorithms that convert raw scan data into usable geometry. These conversions are critical for applications like reverse engineering vintage aircraft parts, performing digital “fit and finish” studies, or even generating complex surfaces for automotive prototypes. As 3D scanning converges with large-format CMM frameworks, the result is a robust system capable of tackling both micro-scale subtleties and macro-scale challenges.
AI, ML, And The Emergence Of Digital Twins
Intelligent Inspection
Artificial intelligence (AI) and machine learning (ML) are rapidly reshaping the metrology field. For example, ML models can analyze measurement data in real time, identifying patterns that human inspectors might miss. This includes detecting emerging wear patterns on tooling or subtle dimensional drift across production cycles. Some advanced CMM software can even predict when a machine needs calibration or maintenance, effectively minimizing unplanned downtime. In complex assembly lines, AI-driven inspection algorithms can be integrated with scheduling and logistics systems, ensuring that parts move seamlessly from one station to another.
The Promise Of Digital Twins
Perhaps the most revolutionary trend is the growing use of digital twins—virtual replicas of physical assets or systems. By leveraging data collected from CMM inspections, businesses can maintain an up-to-date digital twin of their product. This twin can be used for predictive maintenance, where AI algorithms forecast component failures before they happen, minimizing downtime. In addition, digital twins enable sophisticated forensics: in the event of a part failure, engineers can review its entire lifecycle of measured data, identifying exactly when and how the defect emerged. Large-format CMMs are particularly critical in industries where product lifecycles span decades, such as aircraft, where consistent measurement data must be maintained to preserve safety and regulatory compliance.
Relevance In The Age Of Cloud Manufacturing
Cloud Connectivity And Remote Monitoring
The concept of cloud manufacturing has expanded the potential for large-scale CMMs. By leveraging the cloud, manufacturers can store, process, and analyze massive datasets—everything from real-time inspection metrics to historical performance logs. Remote experts can troubleshoot and optimize CMM operations without being on-site, enabling global organizations to centralize expertise. This also allows Original Equipment Manufacturers (OEMs) to push software updates and AI algorithms to distributed CMMs worldwide, ensuring uniform inspection standards and best practices across multiple plants.
Rapid Prototyping And R&D Applications
While large CMMs shine in mass production, they also play an essential role in research and development (R&D). For instance, a prototype of a new aerospace component may require complex geometric verification before flight testing. With the stability and accuracy offered by large-format CMMs, engineers can iterate quickly, validating each design change with data-driven insights. The synergy between cloud-based data management and CMM measurement cycles accelerates this feedback loop, making large CMMs indispensable in cutting-edge R&D environments.
The world of coordinate measuring machines may appear to be undergoing a seismic shift, with portable 3D laser scanners, AI-driven inspection software, and cloud-based manufacturing seemingly challenging the supremacy of traditional, large-format CMMs. In practice, however, these technologies are complementary. Monolithic and gantry-mounted systems continue to set the bar for precision and reliability over substantial measurement volumes, a capability that remains irreplaceable in sectors requiring tight tolerances across large-scale components.
At the same time, the CMM is evolving. Through integration with AI, ML, and advanced CNC software, modern large-format machines offer unprecedented levels of automation, connectivity, and intelligence. They now form critical nodes in smart factory ecosystems, linked to digital twins that facilitate predictive maintenance, real-time feedback loops, and global collaboration. As industries from automotive to aerospace and maritime continue to demand sophisticated dimensional metrology, CMMs—once seen as the hulking behemoths of yore—have proven adaptable, innovative, and, above all, indispensable.
Indeed, the ongoing fusion of large-format CMMs with cloud-based data management, intelligent software, and powerful laser scanning heads ensures that these systems remain at the forefront of industrial metrology. Whether in mass production lines, R&D labs, or complex assembly processes, the modern CMM stands as a testament to how tried-and-true engineering principles can thrive and excel in the digital era.