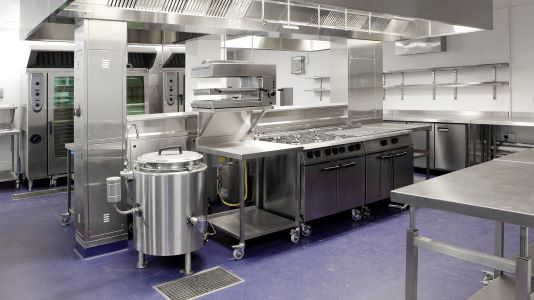
Handheld Laser Welding & Cleaning Technology Addresses Food Industry Challenges
How to increase productivity and create more hygienic food and beverage equipment with IPG Photonics’ handheld laser welding.
From ovens to boilers and from mixing machines to grinders, producing industrial food processing equipment requires a high volume of welding operations. As in any industry, increasing productivity is a chief concern but food and beverage equipment manufacturers must also prioritise hygiene to ensure welds are food grade.
To remain competitive, manufacturers must seek solutions that increase production speeds and minimise the risk of contamination. Handheld laser welding, using laser devices like LightWELD®, has emerged as the ideal solution for many in the food industry as an easy-to-use technology that enables faster, more consistent welds and enables new equipment design possibilities.
Handheld Laser Welding Keeps Things Clean
Industrial food and beverage equipment relies on more than just welds to join part features – manufacturers also make use of fasteners such as nuts, bolts, washers, and rivets. Unlike in other industries, the use of fasteners, as well as threaded holes, must be considered in relation to food contact areas.
Incorrect use of fasteners creates difficult-to-clean geometry that form microcosms for bacterial growth. This risk imposes limitations on how equipment is designed, not to mention increased fabrication costs.
The number of fasteners required in a piece of equipment can only be reduced somewhat by traditional welding methods like Metal Inert Gas (MIG) and Tungsten Inert Gas (TIG), which introduce significant heat input that can damage or distort sensitive features. Laser welding, by comparison, generates considerably less heat during the welding process and is used extensively across industries for thinner metal parts.
This reduction in heat input compared to MIG and TIG opens more fabrication options to designers to help minimise fastener use and reduce material costs. Handheld laser welding also produces very high-quality welds with excellent and hygienic finishes.
The laser welding process is resistant to defects like microcracking, a concern when welding thinner joints using traditional methods, minimising the risk of bacterial growth. Handheld laser welding devices can also be used to spot weld with no part contact required, eliminating common resistance spot welding concerns like bacteria-friendly indentations and asymmetrical welds caused by issues like tip pressure and alignment.
Read more here at page 30
What You Missed:
More Factories Relocate From China To Malaysia Over Restrictions
LG-Hyundai Electric Car Battery Factory To Open On 3 July 2024
Chinese Automakers Double Down On Presence In Thailand
Hitachi Industrial Equipment Systems’ ML Predictive Diagnosis Service For Air Compressors
TSMC Sees Annual Sales Growth To Reach 10% In Semiconductor Industry
Vietnam Versus Malaysia For Semiconductor Design Hub Crown
Vietnam Sluggish Auto Sales Hit Major Motorshow
Motional Flies Solo After Aptiv’s Curtain Call
Tesla Fired Its Supercharger Division – A Shocking Yet Brilliant Move
Tesla Profits Decline By More Than 50% In Q1 2024
WANT MORE INSIDER NEWS? SUBSCRIBE TO OUR DIGITAL MAGAZINE NOW!
CONNECT WITH US: LinkedIn, Facebook, Twitter
Letter to the Editor
Do you have an opinion about this story? Do you have some thoughts you’d like to share with our readers? APMEN News would love to hear from you!
Email your letter to the Editorial Team at [email protected]